Foam is quite literally at the core of every cushioning, padding, or seating project. It’s what provides comfort in many aspects of life, from the soft spring of a bathmat to the bounce of a mattress. Over 1.5 billion pounds of foam are produced and used in the United States each year.
Foam is a key material in automotive and marine seating – an ideal choice for it’s breathability, shaping and rebounding properties. Foam can also be manufactured with antimicrobial additives to preserve durability and cleanliness.
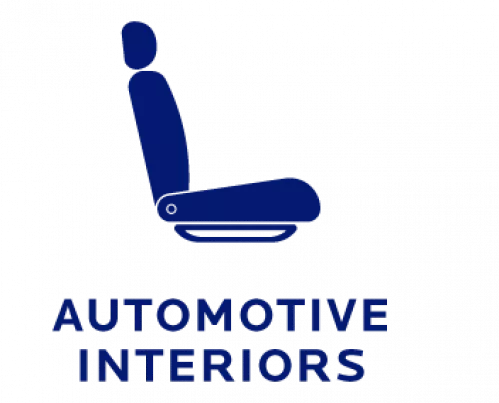
Seating Cushions: Choosing the Right Foam
When used in transportation seating, foam isn’t just applied for comfort, but must be strong enough to protect passengers from floor vibrations while remaining sturdy against the forces of motion and movement overtime.
There are many options for cushioning foam in the market – fiberfill, open or closed cell foam, or various densities of flexible polyurethane foam – so end-use environment and ideal properties are key considerations when choosing materials are key.
Seating can be the most costly component of a vehicle, with demands to contribute to function, comfort and style. It’s important for manufacturers to produce a seat that absorbs and dissipates energy, remains strong against dynamic forces, and delivers on quality from the start. Flexible polyurethane foam is the most widely used foam for automotive seating and trim, as it can be molded to unique shapes while remaining cost effective and dense.
What is FPF?
Flexible polyurethane foam (FPF) is a type of polymer produced by the foaming reaction of polyols and isocyanates through a chemical process pioneered in 1937. The reaction is left to expand and be cut into usable shapes, or is poured into aluminum or resin molds to take desired, more complex shapes. Molded FPF is primarily used in automotive seating, furniture applications, bedding and more.
Antimicrobial Foam for Automotive Seating: What, Why and How?
While any surface can easily become a breeding ground for microbes, automotive interiors experience regular daily contaminants that can aid in the flourishing growth of bacteria, mold and mildew. Single drivers alone can set optimal conditions in place for microbial growth by bringing in dirt, moisture, food and more – let alone the increase in ‘unwanted passengers’ created by pets, children and temperature changes.
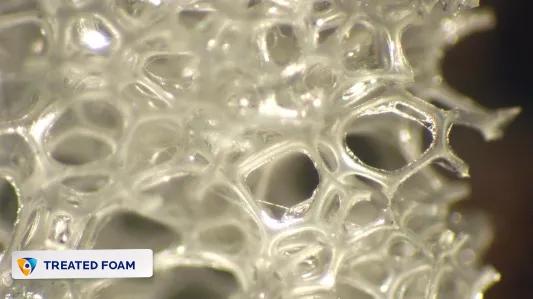
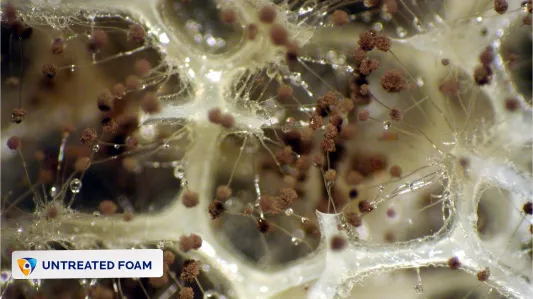
Foam itself provides all requirements for microbes to flourish – its complex structure allows it to collect debris from its surrounding environment, as well as offers plenty of space for spills and grime to be absorbed into the material. Ingredients used to make polyurethane foam can even become food sources for naturally occurring microbes, leading to degradation and odors overtime.
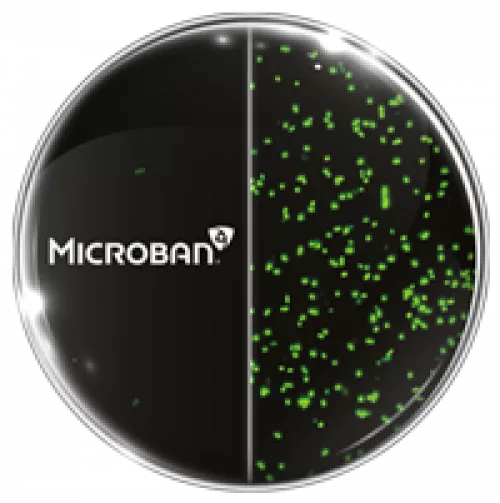
Built-in antimicrobials for FPF and automotive seating
There’s a simple way to enhance and protect polyurethane foam seating from the start, all without interrupting current manufacturing processes: built-in antimicrobial additives. Antimicrobial additives can be seamlessly integrated directly into the liquid polyol stream before the polymerization reaction to become an inherent feature of the material.
By incorporating antimicrobial technologies into the foam from the start, end-use products are protected against the natural growth of bacteria, mold, and mildew 24/7, even in ideal growth conditions. This preventative measure helps to reduce microbial growth before it starts, leaving materials cleaner, fresher and more durable.
Putting Antimicrobial Foams to the Test
Microban International is home to the largest portfolio of customizable antimicrobial formulations that can be tailored to specific end-use applications. Our leading suite of research and development professionals are dedicated to ensuring accuracy and efficacy of our technologies through rigorous testing standards including
- AATCC 30-IV
- AATCC-III / AATCC 174-III
- ASTM G21
- ASTM D3273
- ISO 2743
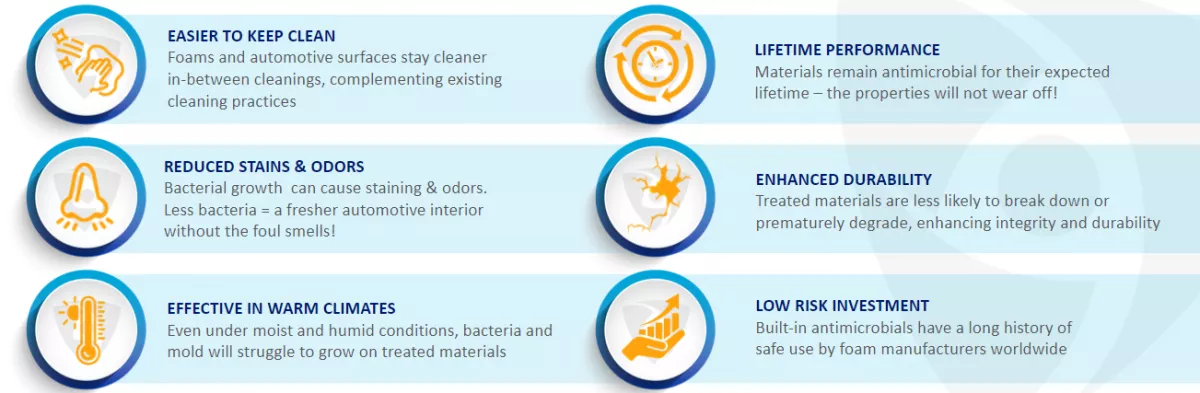