written by Emily Best, North America Marketing Manager at Microban
Who doesn’t love the sight of a healthy little new spring chick? More and more families are beginning to raise their own backyard birds to have their own selection of fresh eggs for meal time, but the poultry industry is still the winner when it comes to meeting the demands of local grocery markets and much of the hospitality industry. The supply chain process between egg laying and the fresh eggs we put onto our plates is vast, and involves various types of equipment, time, egg safety measures, and hard work. Regulations around food and the poultry industry are rigid and strictly enforced, so companies like hatcheries and production houses must have systems in place to ensure compliance and quality at all times to avoid penalties and negative headlines.
This blog will focus on what happens behind the scenes before those cute little spring chicks are hatched. Chickens are hatched from eggs, and those eggs must go through an incubation process in order to stay healthy and allow the chick to develop and hatch correctly. From large industrial hatcheries to smaller local companies, incubation equipment is widely used during this stage of the egg development process to provide an artificial secure environment for chicks to develop inside of eggs and promote egg safety. These incubators provide varying degrees of control such as temperature humidity regulation, egg rotation, air flow and hygiene. Most commercial incubators include plastic trays, moving floors, rollers, or troughs that come into direct contact with the egg during the incubation process.
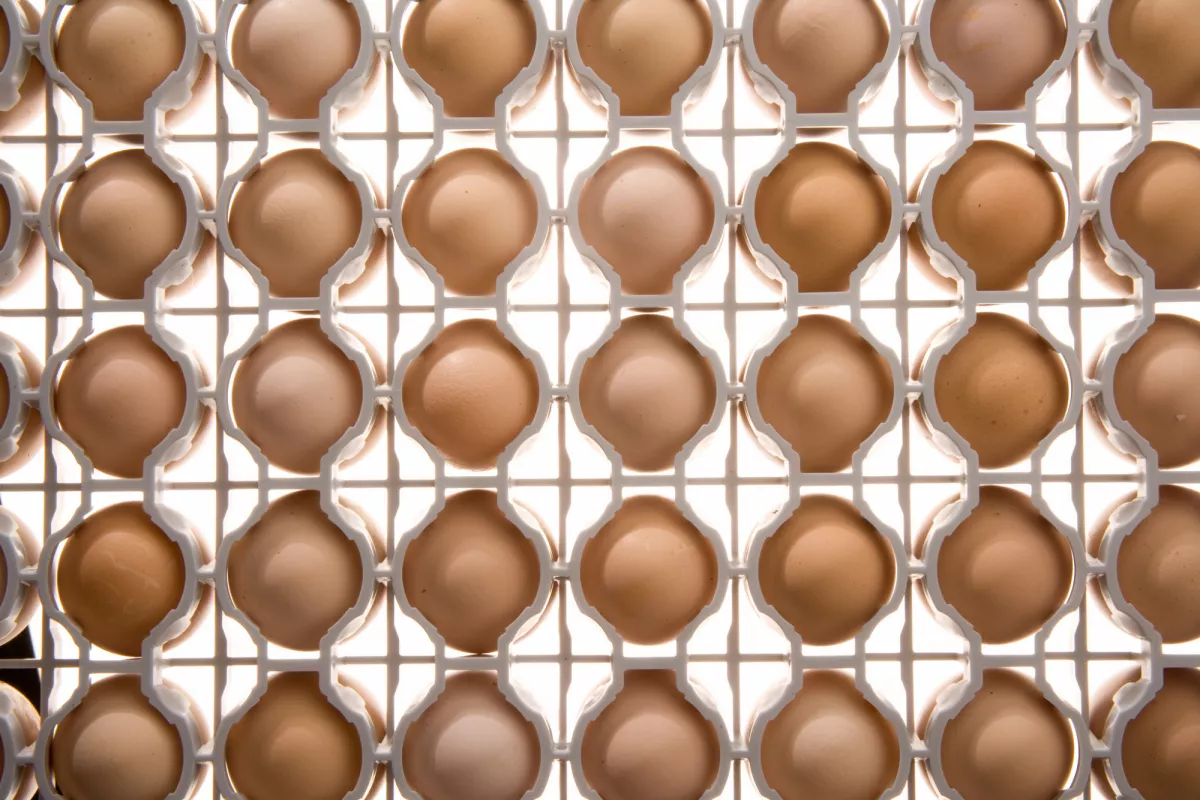
An important fact to note about the incubation process is that eggs are living and breathing, losing water through pores in the shell. Fresh air and the correct humidity levels are vital for the success of the developing chick. During the time, the eggs are susceptible to infection (learn more in about this in Poultry Science) which is why a clean and disinfected environment is crucial. This warm, wet environment inside of incubators provides the perfect breeding ground for bacteria, and if not cleaned properly can harbor germs that will likely have a negative and harmful effect on future hatches. One proactive approach to aid the egg safety journey during incubation is for hatcheries to use equipment that is imbued with bacteria growth inhibiting technology, which can lead to higher hatch rates. Microban is partnered with many companies in the food industry and egg industry that have enhanced their product lines with built in antimicrobial technology that keeps systems cleaner between cleanings, making equipment easier to clean and improving overall durability.
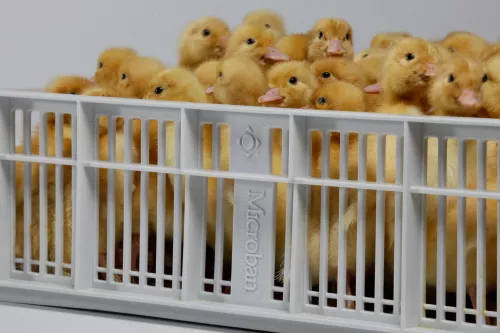
By incorporating Microban technology into hatchery consumables such as setter trays and hatcher baskets, Pas Reform has created a unique and highly effective means of combating cross-contamination in modern hatcheries. Contact with the Microban treated polymer fatally disrupts the biological function of bacteria, to provide continuous protection between wash cycles. Pas Reform products like the SmartStart™ hatcher basket provide a proactive approach to hygiene-critical hatchery consumables.
The COOL EGGSPRESS™ Egg Transport System is the newest and most dynamic innovation for the egg industry in years, engineered to meet current and future regulatory requirements and ultimately save time and money with the use of innovative design and materials. Microban antimicrobial product protection is now also an option on new systems, providing an additional level of protection against the growth of bacteria.
If your company operates in the poultry industry space, contact a member of the Microban team today to learn more about how our technologies can enhance your products and protect surfaces from the growth of potentially harmful bacteria and degradation.